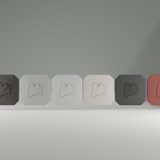
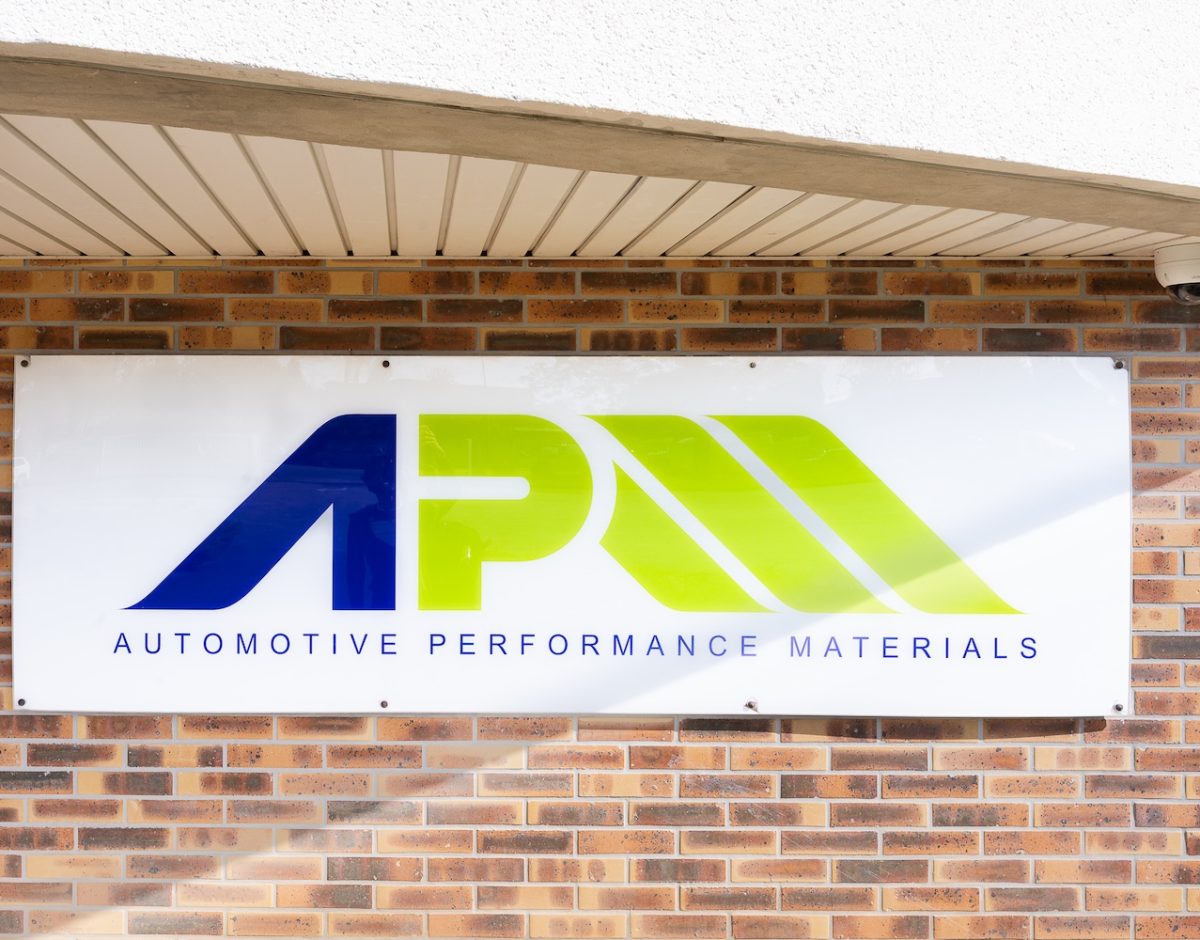
Quand les déchets plastiques, le chanvre ou les fibres de feuilles d’ananas se transforment en tableaux de bord et en intérieurs de voiture flambants neufs pour un bilan carbone inférieur de 85 % à celui du plastique vierge.
Les plastiques vierges font partie du problème. Dérivés de l’industrie pétrolière. Coûts énergétiques et carbone élevés. Difficilement recyclables et finissant encore trop souvent incinérés ou mis en décharge. Face à l’accélération du changement climatique, il est urgent de repenser notre impact environnemental et d’adopter une économie plus circulaire, en commençant par choisir avec soin les produits et les matériaux que nous consommons.
C’est dans cette optique que nos équipes se sont donné pour mission de créer des matériaux haute performance pour l’industrie automobile à partir de déchets recyclés et de biomasse. Notre objectif étant de diminuer de 85 % les émissions de GES nécessaires à la fabrication de nos matériaux d’ici à 2030.
On vous révèle l’essentiel dans cette vidéo — et on vous explique tout dans le détail après !
Passer d’une simple bouchon de bouteille de lait ou d’une tige de chanvre à un tableau de bord automobile relève d’un long parcours semé d’embûches.
Prêt à embarquer ?
Nous collaborons étroitement avec des acteurs clés du recyclage, tels que PCR aux États-Unis et VEOLIA en Europe, pour garantir un approvisionnement stable et de haute qualité en plastique usagé (tant industriel que post-consommation). Le polypropylène issu des bouchons bouteilles de lait ou des flacons de shampoing fait partie de nos ingrédients source préférés. Parallèlement, nous travaillons avec des coopératives agricoles comme INTERVAL pour nous procurer du chanvre capable de capter le CO₂. En favorisant les sources locales, nous réduisons l’empreinte carbone et renforçons la traçabilité de nos matières premières.
Contrairement aux plastiques vierges, les plastiques recyclés ont des compositions et des propriétés très hétérogènes. La biomasse est aussi moins prévisible. Le matériau final doit néanmoins être parfaitement standardisé pour répondre aux exigences strictes du secteur automobile (résistance aux UV, aux chocs, etc.). À cette fin, nous avons mis en place notre propre laboratoire pour analyser et caractériser nos matières premières en interne.
Nos équipes conçoivent ensuite des formulations innovantes pour homogénéiser et améliorer les propriétés du plastique recyclé ou de la biomasse. Elles s’appuient pour cela sur des algorithmes d’intelligence artificielle avancés. Nous complétons nos mélanges avec des additifs et des éléments de renforcement — en utilisant par exemple du chanvre à la place de la fibre de verre — cela afin de répondre (et de dépasser) les exigences de nos clients.
Place au mélange ! Il s’agit maintenant de combiner avec précision le contenu recyclé (et parfois la biomasse) avec les additifs pour obtenir un matériau robuste et homogène. Cette étape requiert un contrôle qualité constant et des ajustements en temps réel lors de l’extrusion, pour que chaque lot soit conforme à son cahier des charges.
La dernière étape ? Transformer ces nouveaux matériaux en pièces automobiles via l’injection. Ce processus intègre de nombreux tests pour vérifier que le matériau résiste à des conditions extrêmes (chaleur, froid, etc.) et, surtout, qu’il soit parfaitement adapté aux process machines. Tout cela est fait-maison.
Nous sommes très fiers de ce que nous avons accompli jusqu’à présent. Et des partenariats que nous avons noués. Certes, de nombreux obstacles subsistent avant que le plastique recyclé et la biomasse deviennent le nouveau standard, mais la révolution est en marche !
Le saviez-vous ?
Notre biocomposite NAFILean-R intègre 20 % de fibres naturelles de chanvre dans une matrice de polypropylène entièrement recyclé et issu de déchets post-consommation. Développé et fabriqué par MATERI’ACT, en partenariat avec Veolia et APM, ce matériau réduit les émissions de CO₂ de 73 % et est 20 % plus léger. Le tout sans compromettre la résistance, la sécurité en cas d’impact ou la qualité de l’air en cabine. Et pour couronner le tout, il est 100 % fabriqué en France !